When a London couple asked local architecture firm Office S&M for an extension that was totally different from the rest of their late-1800s property, cofounders Catrina Stewart and Hugh McEwen took the idea and ran really, really far with it. The new addition's facade isn't just modern in comparison to the client's historic house, but in comparison to even the most contemporary home. We've never seen anything like it until now, and that's saying something since it's our job to know about these things. What are we talking about, exactly? The extension's exterior isn't covered in brick or stucco or clapboard; it's coated in spray-on rubber.
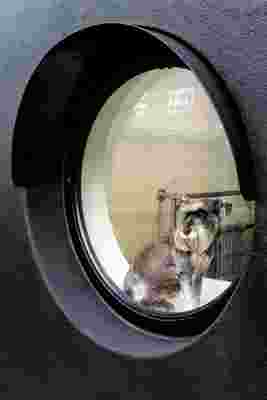
The client's pup has the best seat in the house.
Office S&M did not, in fact, make this finish up. It's just that the material, called Prokol , was developed for use on oil rigs, says Hugh, so it's gone mostly unnoticed in the residential construction world. "It was a material we had been interested in using for a long time, since it is rarely used in a residential setting and we had only seen it used on art projects," he explains. "We had seen other housing projects that used sheet rubber, so knew it would work in principle, but none of those had used a spray-on finish. The client was really excited by the seamless finish that could be created, and we designed the outside of the house to be as slick as possible." Cue the single quirky round window and minimalist metal-frame glass door.
Another benefit: the cost. "Since we wanted to make the most of the client's tight budget, we only suggested materials that were very cost-effective," says Hugh. "The cost of the entire exterior, including all walls and the roof, for the supply and professional installation was just over £4,000."
How the heck does one apply rubber to a house? Apparently, with a tricked-out hose, as if the finish wasn't futuristic enough already.
Content
Hugh gave us a step-by-step rundown of the process: "When the timber work was completed, the installation began with a primer being applied to the entire surface by hand. This was left to dry in order to provide a really good bond," he explains. A team of three from contractor ESW then arrived to apply the actual rubber. "The material is held at high temperature in a van-size tanker, where it is pressurized and fed through a hose to the operative who is applying it," says Hugh. "Since it is a two-part epoxy, the separate parts are mixed together in a specialized spray nozzle, where they emerge as hot, high-pressure droplets. As soon as they hit the application surface, they cool instantly, so there is quite an art to the application. This required the team to have one person spraying, one member checking the install, and one attending the tanker and pressure system."
Oh, but it probably requires sooo much upkeep , you're thinking. Nope. "It doesn't require any care," Hugh says. After all, the finish is primarily for commercial boats, which we can imagine see a ton of wear and tear. "We designed the exterior detailing in response to this, since it can shed water without any fussy waterproofing details. The material is UV-stable, completely weatherproof, and even comes with a 30-year guarantee." We've officially started the hunt for a similar finish Stateside.